1:1 Interactive Architecture
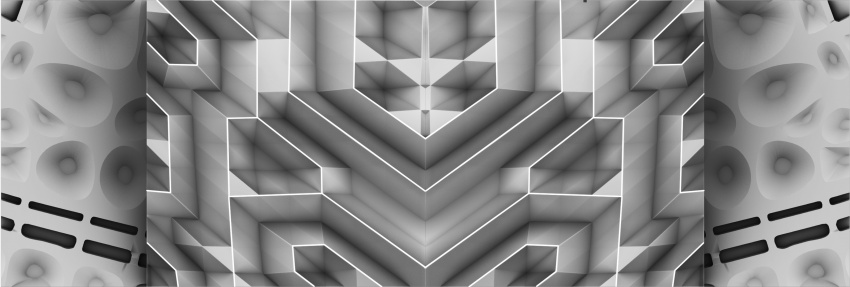
Introduction
This project emanates from the TUD proposal to the European Space Agency (ESA) for the creation of an Off-Earth structure utilizing Martian regolith. The primary goal is to establish a protective underground habitat on Mars, shielding astronauts from the inhospitable environment. The proposed methodology involves deploying mining robots to excavate the terrain, forming underground caves that offer insulation against extreme temperatures and radiation. Subsequently, a swarm of autonomous mobile robots is tasked with utilizing Mars’s resources to process building elements.

My research is centered on refining the building system outlined in the proposal, focusing on the excavation and formation of burrows. I conducted a structural analysis of a specific shell, targeting a complex junction where multiple surface curvatures converge, giving consideration to the forces involved. This exploration is essential for developing a building system capable of generating surfaces against gravity while ensuring airtightness, thermal insulation, and acoustic comfort.

Structural Analysis of excavated Regolith layer:
For the structural analysis, we analyzed the shape using the surface loading conditions as per te ESA proposal. The study was done with finite element analysis from Karamba and Millipede plugins. Although it was challenging to get the exact material properties of regolith, the features of concrete were used as an equivalent alternative. The results indicate tension in the more projecting parts of the fragment compressive forces at the more recessed parts of the fragment. The stress lines generated by the millipede script cross verify this as well. Based on the results of this analysis, it can be inferred that parts in tension would deform outward as indicated in the Karamba Analysis, making the excavated surface highly unstable and hence requiring some form of reinforcement. The stress lines generated by the Millipede script indicate the most optimum positions where the reinforcements in the form of robotic stintering can be done on the surface of the regolith.


Reinforcing the structural Martian Regolith layer:
Laser sintering Technology for in-situ additive manufacturing is being researched by the Johnson space center in Texas, USA. This is one of the manufacturing process that has been proven to qualify as a possible solution to utilize materials in-situ in Lunar or Martian contexts. Laser sintering is a process that fuses layers of powdered metal by melting the metal at the right temperature that fuses these layers together, see figure 10. Most important factors to be considered for the resultant structure is the heating time and temperature. The aim of this design is to use this technology to strengthen the excavated shell in the martian ground. As martian regolith is a fine soil that resembles the texture of desert sand on earth. It becomes vital to reinforce martian regolith during the excavation process in order to hold it place and prevent the shell from caving in.
Therefore, to reinforce the fine regolith, the design envisions the use of laser sintering to melt the constituents of martian regolith to produce a layer of metal, increasing the density of the material and creating a stronger outer surface, hence strengthening the excavated regolith layer.

Silicon layer for air-tightness:
NASA’s Curiosity rover in 2015, discovered large concentrations of Silicon deposits in lighter coloured rocks on Mars. This discovery has increased the hope of creating Martian habitats, as Silica aerogel can mimic Earth’s atmospheric Greenhouse gasses. However, in this preliminary design proposal, a layer of silicon is proposed to seal the structural regolith layer and act as an air-barrier. This barrier ensures thermal insulation and air-tightness. The proposal envisions this layer to be additively manufactured by a robotic arm with an end-effector that mimics the working of a caulking gun.
Structural connection between the two layers:
The connector element is designed in such a way that it connects the additive acoustic layer to the subtractive regolith layer, while ensuring air tightness between the two layers with the help of a silicone layer that is printed on the sintered surface. This connection will be 3D printed on site somewhere at a distance away from the excavation and will be made out of metal that is found in Martian Regolith. There are two main components of the connector (Metal conenctor and Metal sleeve) which uses the principle of a male-female snap joint.

Design of Acoustic Layer :
Reaction and diffusion of chemicals can produce a variety of patterns, reminiscent of those often seen in nature. The advantage of using a simulation reaction is that it is possible to control it when it will maintain a certain organic randomness. The Gray Scott equations model is a simulation of such a reaction. And a part of this model forms the basis of the shape of the acoustic panels. The reaction works with the input of two different liquids, that are able to be controlled by the simulation. The ratio of these liquids creates a pattern with dots or stripes. The scale of the reaction is customizable by changing the size of the mesh. As well as the depth of the surface. The fig (29) illustrates the search for an acoustic functional panel based on the Gray Scott model.


